John Barrett, Peter Taylor, Jonathan Norman and Jannik Giesekam
Introduction
Industry ultimately provides all the goods and services demanded by UK households, from major infrastructure to mobile phones. This clearly uses energy that leads to greenhouse gas (GHG) emissions. In fact, UK industry accounts for 16% of total final energy demand and 23% of the UK’s GHG emissions (BEIS, 2017a; CCC, 2018). Since 1990, industrial GHG emissions have nearly halved, with 85% of this reduction occurring between 1990 and 2010. The reductions since 2010 have been more modest, with emissions actually increasing by 1% in 2017 (BEIS, 2017b). The reduction in emissions has been due to a complex mixture of structural change within UK industry, greater reliance on imports to meet the demand for energy intensive industrial products, changing demand for industrial products, and improved energy efficiency (Hardt et al, 2018; Hammond et al, 2012).
Industry is a diverse and heterogeneous sector and there are numerous ways to describe its structure and to identify opportunities to improve energy efficiency. For example, Griffin et al, (2016) identify 350 different combinations of technologies and sectors relating to industrial energy demand. This makes it challenging both to identify appropriate options and to propose generic solutions. Other studies consider industry from a resources and materials perspective, such as steel, cement and paper for example (Owen et al, 2018; BEIS, 2015. Industrial roadmaps for a number of industrial sectors are available from GOV.UKOpens in a new tab). When identifying mitigation options it can be misleading to treat industry as a single sector. Instead, it is necessary to disaggregate by subsector and identify current and available technologies, material and product outputs, trade patterns and infrastructures (Barrett et al, 2018).
Direct GHG mitigation options for industry are often grouped into four categories: improved energy efficiency, fuel switching, electricity decarbonisation and carbon capture and storage (Griffin et al, 2016). Clearly, there is role for all these options, however this chapter focuses on the role of energy efficiency in industry itself, plus broader measures to reduce energy demand from changing the mix of, and demand for, materials, products and services.
We achieve this by identifying the historical trends in UK industrial energy demand and explaining the reasons behind them. We review the current UK Government policy approaches as outlined in the Clean Growth Strategy and then consider whether there could be a more ambitious role for both industrial energy efficiency and broader options for reducing energy demand such as material efficiency. Before proposing some recommendations to reduce industrial energy demand, we explore the level of ambition needed in UK industry in relation to internationally agreed climate targets.
Recent trends in industrial energy efficiency and demand
A simple examination of historical trends in UK industrial energy demand suggests a major success story. While UK GDP has grown by ~70% since 1990, industrial energy demand has fallen by ~40% – indicating an absolute decoupling between the two (see Figure 5).

Reductions in industrial energy use have been greater than the average for all sectors in the UK. One of the reasons for this is a decline in the amount of energy used per unit of industrial output – known as energy intensity. Sometimes this metric is used as a proxy for energy efficiency, but this is misleading. It is influenced by a range of factors, including changes in the mix of industrial sectors and industrial products. For example, a shift away from heavy industry and towards consumer electronics would tend to reduce energy intensity. Hence, reductions in industrial energy intensity are not only a result of improvements in the technical efficiency of industrial processes.
Hardt et al, (2018) estimate that between the period of 1997 to 2013 half of the reduction in industrial energy intensity can be attributed to improvements in technical energy efficiency, with the rest being due to structural change and other factors.
Structural change, in turn, includes both changes in the mix of industrial sectors, and changes in the mix of domestically-produced versus imported goods and services. Since 1990, there has been a trend towards ‘offshoring’ industrial production to other countries, meaning that a smaller share of the goods and materials consumed in the UK are produced in the country. Figure 6 demonstrates that offshoring was the most important factor along with energy efficiency improvements between 1997 and 2013. While the offshoring of industrial energy use helps meet national GHG emission targets, it fails to deliver a global reduction in emissions.
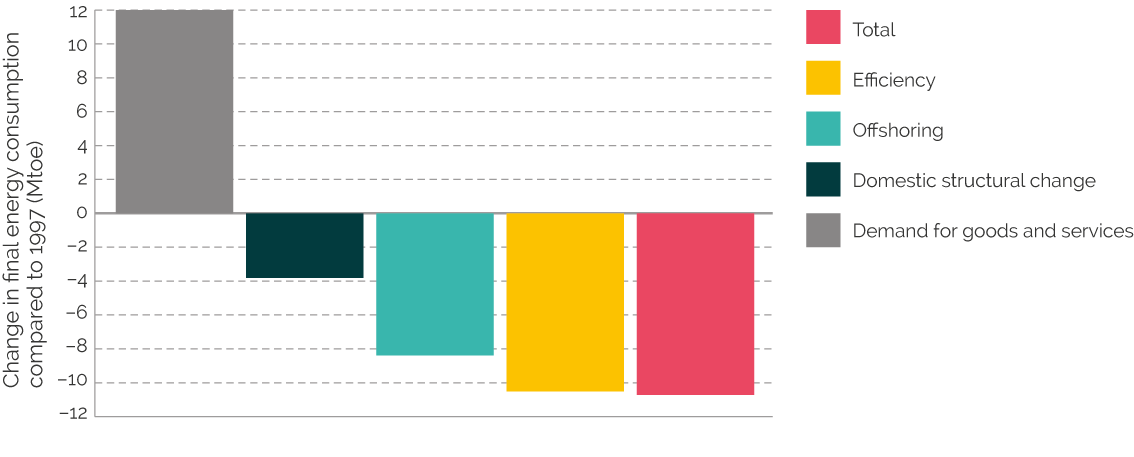
In the more recent period from 2007 to 2013, the growth in demand for goods and services from industry resulted in increased energy demand. This increase was only partly offset by a reduction in energy demand from improved energy efficiency over the same time-period. Therefore, without the reductions from domestic structural change and offshoring, industrial energy demand in the UK would have been marginally higher in 2013 than in 2007.
Current approaches to delivering industrial energy demand reduction
The Clean Growth Strategy (CGS) sets out a range of strategies to help decarbonise industry, including not only energy efficiency and demand reduction but also fuel switching and other abatement options. On energy efficiency, it sets a high-level goal for improvement across business and industry of at least 20% by 2030 and outlines a number of strategies to deliver this. From an historical perspective, this represents a ‘business as usual’ ambition with the level of improvements being similar to those seen in the past.
The CGS analysis (BEIS, 2017b) shows that overall industrial emissions savings in the region of 45MtCO2 are technically possible by 2050 compared to baseline emissions in that year (CO2 emissions being 123MtCO2 from industry in 2015). This 37% reduction would be mainly achieved through carbon capture, usage and storage (CCUS) and fuel switching, with a very small role for energy efficiency of 5MtCO2 (4% of 2015 emissions).
It is unclear when these reductions would be delivered and the issue of timing is extremely important when considering cumulative emissions, and therefore impact on climate. The Committee on Climate Change (CCC) however suggest that this 5Mt reduction relates to energy efficiency that could be achieved by 2030. However, this 5 Mt emissions saving may not be the total contribution to GHG reduction from energy efficiency, since the BEIS baseline projection already incorporates some energy efficiency improvements – based on extrapolating past relationships between energy use and GDP. This makes it difficult to assess what the total contribution by 2050 from energy efficiency might be. However, the impression given in the CGS is that the role of energy efficiency is expected to be minimal compared to other options.
The CGS and numerous other publications identify multiple economic barriers to achieving energy efficiency improvements such as split incentives, asymmetric information and high transaction costs. Therefore, it is difficult to reduce energy demand without some policy intervention as the business case for further improvements is weak, especially in the energy intensive sectors. A number of strategies are therefore outlined in the CGS to meet the high-level energy efficiency goal, building on the ‘Industrial Decarbonisation and Energy Efficiency Action Plans’ (BEIS, 2017c), and the earlier roadmaps (BEIS and DECC, 2015). The proposed strategies include: an Industrial Energy Efficiency Scheme providing support for large companies to invest in energy efficiency; increasing the Climate Change Levy rates after 2019; improving and reforming the Energy Savings Opportunity Scheme (ESOS); introducing a new energy and carbon reporting framework for business to replace existing schemes; and dedicating £18m to industrial heat recovery (BEIS, 2017b). In addition, the CGS proposes a funding framework for R&D in industrial decarbonisation, with £162m to be invested by 2021 (BEIS, 2017b) on a range of projects covering energy, resource and process efficiency, better low carbon fuels and CCUS. The Industrial Strategy Challenge Fund additionally has the ‘Transforming Foundation Industries Challenge’, covering glass, metals, cement, ceramics and chemicals. However, the CGS provides little detail on the design and implementation of these strategies and it remains unclear how they would collectively deliver significant reduction in GHG emissions in line with UK and global ambitions.
Ultimately the success of these schemes will come down to the detail of their design and implementation, including the ability to target the most cost effective measures and to reduce the associated transaction costs. Learning from other countries is essential here. For example: Canada has introduced an industrial energy efficiency programme in four provinces; Denmark has established a ‘Secretariat for Energy Savings’, targeting industry with information-based measures providing assessment and analysis of energy use (IEA, 2017a; IEA, 2017b); the Netherlands has a system of ‘Long-term Agreements’ with industry; Germany has an energy efficiency framework, which has been highly effective at reducing energy intensity; and Japan has had their ‘Top Runner Programme’ since 1999, orientated towards the manufacturing sector (Geller et al, 2006; IEA, 2016; IEA, 2013; IEA, 2014).
We now consider what a successful programme could potentially deliver in relation to energy efficiency and whether there should be an increased level of ambition.
Energy efficiency options in industry
Energy efficiency is often seen as ‘the first fuel’, delivering cost saving as well as delivering environmental benefits. It is seen as highly attractive because it does not necessarily rely on changes to behaviour and lifestyles and allows the continuation of existing business models. Therefore, is the CGS right to identify such a small role for energy efficiency in industry to deliver GHG emission reductions?
The CGS analysis draws from a road-mapping exercise for eight sectors of UK industry (WSP, Parsons Brinckerhoff and DNV GL (2015)) and concludes that, under a scenario of incremental improvements, energy efficiency could annually contribute 5.3 Mt CO2 savings by 2050 (4% reduction as noted above). Under a scenario of ‘maximum technology’, which ignores economic and commercial considerations, and includes technologies currently at low technology readiness levels, this figure increases to 7.6 Mt CO2 (6% reduction).
Energy efficiency saving potentials were found to be lowest in percentage terms in energy intensive sectors, such as iron and steel, and cement manufacture, which aligns with the findings of other work (Griffin et al, 2014). This is consistent with the observation that energy efficiency improvements within energy intensive sectors have been plateauing in recent years (Hammond and Norman, 2016). The high share of energy in overall production costs of these sectors has driven energy efficiency improvements for decades, and so the remaining potential may be relatively small and difficult to realise. For example, it is widely acknowledged that several energy intensive industrial processes (such as steel production) are close to what is technically feasible in relation to energy efficiency (Norman et al, 2016). This broadly leaves two options for these sectors: radically different industrial processes as envisaged by the CGS and/or changes in demand for their products.
Options such as CCUS have yet to become economically viable and are unlikely to be implemented at scale in the short term. Rapid reductions in cumulative emissions to meet internationally agreed climate targets require changes in the next decade.
Conversely, the non-energy intensive sectors, having historically not had such strong drivers to improve efficiency, may have relatively greater opportunities remaining (often referred to as ‘low-hanging fruit’). There is limited evidence of where such potential might lie as these non-energy intensive sectors represent a challenging area for analysis, with poor data availability and highly heterogeneous uses of energy (Griffin et al, 2016). The potential for opportunities related to ‘cross-cutting technologies’ used in multiple sectors of industry (such as boilers and motors) are often relied on to assess the emissions reduction opportunities in non-energy intensive sectors. This leads to an incomplete analysis of the improvement opportunities by not representing the diversity of energy-using processes and efficiency options. Examples of particularly complex sectors include food and drink, textiles, chemicals and engineering. More evidence is needed to ensure a thorough appreciation of the opportunity in the non-energy intensive sectors.
In conclusion, the level of ambition for industrial energy efficiency identified in the CGS should be increased. However, it is highly unlikely that dramatic gains are going to be possible in the short term. The most promising area for further rapid action may be the non-energy intensive sectors, but they also represent a smaller proportion (~35%) of total energy demand. Realising major additional improvements in the energy intensive sectors will require significant process change and therefore capital investment, which is unlikely to materialise in globally competitive markets without significant Government support.
Therefore, identifying opportunities for sustained reductions in industrial energy use to 2050 also requires an understanding of how to reduce demand for the most energy intensive materials and products, which we explore in the following section.
Going beyond energy efficiency to reduce industrial energy demand
All energy demand in industry ultimately relates to goods and services provided for households and government. With limited options available to reduce energy demand through efficiency improvements, changing demand for the goods and services produced by industry offers further mitigation options. Energy is embodied in products as raw materials (e.g. minerals) are processed into useful materials (e.g. glass and metals) and manufactured into products (e.g. buildings, cars and electronics) which in turn are used as inputs to all intermediate sectors (e.g. agriculture, construction, transport and financial services) or sold to final consumers (e.g. households and government) (Scott et al, 2018). As ‘carriers’ of industrial energy, the trade of materials and products results in the transfer of embodied energy between sectors, countries and consumers (Scott et al, 2018). Figure 7 shows how UK and international energy supply flows (through materials) from the energy system, to industry and to final consumers of products in the UK, commonly defined as the UK’s consumption-based GHG accounts (Latest data for the UK is available from: GOV.UKOpens in a new tab).
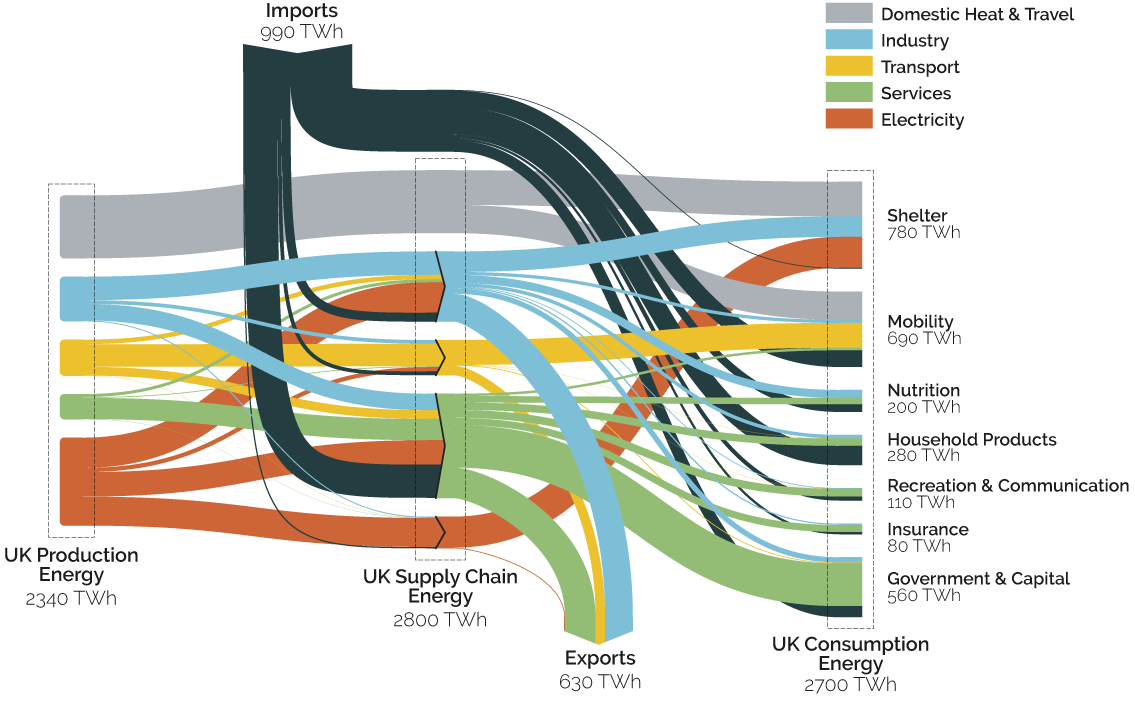
Image description
UK energy production totals 2340 TWh, backed up with 990 TWh of imported energy. 2800 TWh go into the UK supply chain, with 630 TWh exported. UK consumption energy totals 2700 TWh, broken down into: shelter 780 TWh, mobility 690 TWh, nutrition 200 TWh, household products 280 TWh, recreation & communications 110 TWh, insurance 80 TWh and government & capital 560 TWh.
The left of the figure shows the energy demand of the UK (2340 TWh) for five sectors. The UK imports a further 990 TWh of embodied energy in materials that are imported either into industry (intermediate demand) or as final product to consumers (household demand). It also exports 630 TWh, making the UK a net importer of embodied energy. On the far right of figure 7 is the energy embodied in household services such as shelter, mobility and nutrition.
The value of this analysis is the ability to identify additional mitigation options beyond energy efficiency. These could be broadly described as ‘Putting Less In’ (production changes) and ‘Getting More Out’ (consumption changes) to change our use of materials and products that ultimately reduces the need for industrial energy. Production changes could include reducing waste in industry, lightweighting products and packaging, fabrication yield improvements, modular design or remanufacturing. Consumption changes could include household reductions in waste, shifts from recycling to refurbishing, using products longer, accessing services as opposed to ownership (car clubs for example) and sharing (higher occupancy rates in vehicles and buildings). Indirectly, all these changes have the potential to reduce industrial energy demand.
Scott et al, (2019) calculated the potential for material efficiency across seven sectors (see table 1), considering measures that include waste reduction, lightweighting of products, material substitution and product longevity.
Sector | Putting less in (production) | Getting more out (consumption) |
---|---|---|
Clothing & textiles | Reduce supply chain waste through efficiency improvements in fibre and yarn production, dyeing and finishing. | Dispose of less and reuse more. Dispose of less and recycle more. Use for longer. |
Food & drink | Reduce avoidable food waste in food services and hospitality sectors. | Reduce avoidable household food waste |
Packaging | Reduce weight of packaging (metal, plastic, paper, glass). Waste prevention. |
n/a |
Vehicles | Reduce steel, aluminium and additional weight without material or alloy changes. Yield improvement (metals) in car structures through cutting techniques. Steel fabrication yield improvement Reuse discarded steel products. |
Shift from recycling to refurbishing. Car clubs. Use cars longer. |
Electronics, appliances & machinery | Reduce steel without material or alloy changes. Steel fabrication yield improvement. Reuse discarded steel products in industrial equipment. |
Sharing less frequent electrical appliances (e.g. vacuum cleaners), power tools and leisure equipment. Use for longer. Remanufacturing instead of throwing away. |
Construction | Design optimisation to reduce material inputs. Material substitution. Material reuse. |
n/a |
Furniture | Reduce steel without material or alloy changes. | Dispose of less and reuse more. Dispose of less and recycle more. |
Collectively, these options offer a greater potential for emission reduction by reducing energy demand than all the current planned reductions in industry documented in the Clean Growth Strategy related to energy efficiency in industry (5 Mt CO2 in 2030). These material efficiency options offer potential savings of 21 Mt CO2 in 2030. The material efficiency measures documented in Scott et al (2019) represent a conservative assessment of the potential for emission reduction and are by no means the maximum potential. They rely on evidence from existing case studies and therefore once the UK started on a path towards material productivity further options are highly likely to emerge.
One of the key advantages of material efficiency strategies relates to timing. The reality of climate change is that it is the total cumulative GHG emissions that relate to temperature rises, meaning that reductions in the short term offer significantly more investigation potential, especially if the changes create a long-term change. Many of the material efficiency strategies listed above require no major breakthrough in technology and limited capital investment but do need Government intervention to ensure that they materialise.
The other advantage of these measures is that GHG emissions are not just reduced within the UK but would reduce emissions in other countries. The UK is a large importer of energy intensive materials and many of the strategies would reduce the UK’s reliance on imports. While the analysis above only lists the emissions savings that would occur in the UK, other studies suggest that a similar, if not greater reduction, would occur in other countries as a result of UK action (Barrett et al, 2013). This reinforces the notion that the UK could become a global leader in tackling climate change while also reducing its reliance on imports.
Conclusions and recommendations
Industry is often considered a hard to mitigate sector and most emissions scenarios allocate a larger proportion of the carbon budget by 2050 to industry because of this. Under such scenarios further and faster emission reductions are required in other sectors to allow for the additional ‘carbon space’ allocated to industry. At the same time, demand for industrial energy has not declined as rapidly as may appear from national energy data, because some of it has simply been offshored, with no benefit for global efforts to reduce emissions.
The current UK Government strategy is framed around achieving an 80% reduction in GHG emissions by 2050 (based on 1990 levels). It is clear that this target is inconsistent with international efforts to reduce GHG emissions to net-zero in the 2050s, and therefore the UK Government is currently considering a net-zero target by 2050, in which case industry emissions would need to be much closer to zero than is currently assumed. Under this framing, choices between energy efficiency or fuel switching or CCUS disappear. The required framing is energy efficiency and fuel switching and CCUS and a comprehensive assessment of changing consumption patterns to reduce the needs for materials and products. With material efficiency measures potentially being three to four times more significant in reducing emissions than energy efficiency options, there is an urgent need to ensure that the Waste and Resource Strategy aligns with the CGS.
The good news is, collectively, these options could deliver substantial reductions ensuring that industry does not require a favourable allocation of future carbon budgets over other sectors. However, the efforts to achieve these reductions should not be under estimated, requiring additional policy and strong partnerships between the UK Government and industry. Without Government intervention they will simply not be realised. This requires alignment not just in climate and resource efficiency strategies but more broadly with economic objectives and future industrial strategy. With responsibilities cutting across Government departments (in particular Treasury, Business, Energy & Industrial Strategy, Ministry of Housing, Communities & Local Government, and the Department for Environment, Food & Rural Affairs), a joined-up, coherent and comprehensive plan is required. This plan is urgently needed to accompany the CGS, along with clarification of the rather vague measures currently proposed.
What all these schemes have in common is the need for high quality data, benchmarking and metrics to enable successful targeting, monitoring and measurement. At present, the UK lacks the data and institutional framework to deliver such a programme. Data on energy consumption linked to industrial processes is very poor, with economic data often being used to derive proxies for energy use. This makes assessments of progress and potentials very difficult, with non-energy intensive sectors being particularly poorly understood. The first step to implement an energy and material efficiency scheme for industry is to establish the necessary structures around data and management. This ensures that a transparent platform is in place for Government to engage in a transformative plan with UK industry to deliver a net-zero target by 2050.
In summary, our key recommendations are as follows.
- We recommend that Government increases the ambition for energy demand and emission reductions goals in industry (BEIS). These needs to align with internationally agreed targets and goals for net-zero emissions.
- We recommend that Government adopts industrial energy-use goals that include energy efficiency, fuel switching, process decarbonisation, CCUS and reducing the demand for materials and products (BEIS, Defra, Devolved Governments). The savings potentials to deliver stronger goals exist, but delivering them requires a more holistic approach, including energy efficiency and fuel switching, but also going further to include demand for materials and products for short-term reductions and transformative technologies for longer-term gains.
- We recommend that Government develops a comprehensive industrial energy demand policy, providing support and incentives for innovation and deployment of new technology and business models, including for energy efficiency and material efficiency by final consumers (HMT, BEIS, Defra, Devolved Governments). The scale and pace of change required is not going to happen by itself and therefore needs more policy intervention. This needs to involve Government playing an active role in supporting innovation and creating markets, including by ensuring that their own procurement patterns reflect the changes needed.
- We recommend that Government accepts the need to address questions of lifestyle and behaviour change to deliver energy and material efficiency (HMT, BEIS, Defra, Devolved Governments). The options for energy efficiency improvement in the energy intensive sectors are very limited in terms of emission reductions, in the short term. Therefore, the UK Government needs to openly recognise that technology alone will not be enough and initiate a public debate on our lifestyles and their lack of consistency with a net-zero future.
- We recommend that Government develops a cross-Government approach to energy, climate, waste and industrial strategy (Defra, BEIS, Devolved Governments, HMT). This is needed to ensure that investment support, tax regimes and strategies are aligned. Energy, climate and waste policies need to be seen as integral parts of an economic policy that provides the right incentives to guide and support industry.
- We recommend that Government aims to take a leadership position internationally on energy intensive material supply chains (BEIS, Defra, DIT, FCO, DfID). With the UK being heavily reliant on imported energy intensive materials and products, the UK Government must work internationally to reduce the energy and associated emissions of international supply chains.
- We recommend that Government works with industry and the research community to develop and share better industrial energy and materials data (BEIS, Defra). Given the far-reaching nature of the changes, policies need to be evidence-based. Data availability and quality are currently not good enough for the level of analysis that is needed. Uncertainty is too high and not enough is known. An investment in more robust and transparent industrial energy data linking energy demand with key processes and infrastructure to allow more accurate benchmarking of sectors, materials and products is urgently required.
References
Show all references
- Barrett J., Scott K. (2013). Link between climate change mitigation and resource efficiency: A UK Case Study. Global Environmental Change, 22: 299–307. doi: 10.1016/j. gloenvcha.2011.11.003
- Barrett J., Scott K., Owen A. & Giesekam J. (2017). Invisible energy policy – analysis of the link between consumption and energy demand. Proceedings of the 4th Sustainable Thermal Energy Management International Conference, pp. 198–205.
- Barrett, J., Cooper, T., Hammond, G.P., & Pidgeon, N. (2018). Industrial energy, materials and products: UK decarbonisation challenges and opportunities. Applied Thermal Engineering, 136 (1): 643–56. doi: /10.1016/j. applthermaleng.2018.03.049
- CCC (2018) Reducing UK Emissions – 2018. Progress Report to Parliament, pdfOpens in a new tab
- BEIS and DECC (2015). Industrial Decarbonisation and Energy Efficiency Roadmaps to 2050Opens in a new tab
- BEIS (2017a). Digest of UK Energy Statistics – 2017, National Statistics PublicationOpens in a new tab
- BEIS (2017b). Clean Growth Strategy, pdfOpens in a new tab
- BEIS (2017c). Updated Energy and Emissions Projections – 2017, pdfOpens in a new tab
- Griffin, P. W., Hammond, G. P. & Norman, J. B. (2014). Prospects for emissions reduction in the UK cement sector. Proceedings of the Institution of Civil Engineers – Energy. 167 (3): 152–61. doi: 10.1680/ener.14.00007
- Griffin, P. W., Hammond, G. P. & Norman, J. B. (2016). Industrial energy use and carbon emissions reduction: a UK perspective. WIREs Energy Environment, 2016, 5: 684–714. doi: 10.1002/wene.212
- Hardt, L., Owen, A., Brockway, P., Heun, M., Barrett, J., Taylor, P. & Foxon T. (2018). Untangling the drivers of energy reduction in the UK productive sectors: Efficiency or offshoring? Applied Energy, 223 (2018): 124–133. doi: 10.1016/j.apenergy.2018.03.127
- Hammond, G &. Norman, J. (2012). Decomposition analysis of energy–related carbon emissions from UK manufacturing. Energy, 41: 220–227. doi: 10.1016/j. energy.2011.06.035
- IEA (2013). Energy Policies of IEA Countries: Germany 2013 Review, pdfOpens in a new tab
- IEA (2014). Energy Policies of IEA Countries: The Netherlands 2014 Review, pdfOpens in a new tab
- IEA (2016). Energy Policies of IEA Countries: Japan 2016 Review, pdfOpens in a new tab
- IEA (2017a). Energy Efficiency 2017: Market Report.
- IEA (2017b). Energy Policies of IEA Countries: Denmark 2017 Review, pdfOpens in a new tab
- Norman, J.B., Serrenho, A.C., Cooper, S.J.G., Owen, A., Sakai, M., Scott, K., Brockway, P.E., Cooper, S., Giesekam, J., Salvia, G., Cullen, J.M., Barrett, J.R., Cooper, T., Hammond, G.P. & Allwood, J.M. (2016). A whole system analysis of how industrial energy and material demand reduction can contribute to a low carbon future for the UK, pdfOpens in a new tab CIEMAP report.
- Owen, A., Scott, K. & Barrett, J. (2018). Identifying critical supply chains and products: UK decarbonisation challenges and opportunities. Applied Energy, 210: 632–642. doi: 10.1016/j.applthermaleng.2018.03.049
- Peake L. (2018). Less in – more outOpens in a new tab Report by the Green Alliance and Centre for Industrial Energy, Materials and Products.
- Scott, K., Roelich, K., Owen, A. & Barrett, J. (2018). Extending European energy efficiency standards to include material use: an analysis. Climate Policy, 18 (5): 627-641. doi: 10.1080/14693062.2017.1333949
- Scott, K., Giesekam, J., Barrett, J. & Owen, A. (2019). Bridging the climate mitigation gap with economy-wide material productivity. Journal of Industrial Ecology, 2018: 1–14. doi: 10.1111/jiec.12831
- WSP, Parsons Brinckerhoff and DNV GL (2015). Industrial Decarbonisation & Energy Efficiency Roadmaps to 2050 Cross-sector SummaryOpens in a new tab London, UK.
Publication details
Barrett, J., Taylor, P., Norman, J. and Giesekam, J. 2019. 3. Industry, materials and products. In: Shifting the focus: energy demand in a net-zero carbon UK. Eyre, N and Killip, G. [eds]. Centre for Research into Energy Demand Solutions. Oxford, UK. ISBN: 978-1-913299-04-0
Banner photo credit: Alireza Attari on Unsplash