CREDS researchers share their thoughts on the proposed new coal mine in West Cumbria, which would be the first new deep coal mine in the UK in 30 years.
The proposed new coal mine in West Cumbria, which would be the first new deep coal mine in the UK in 30 years, has received considerable levels of media attention in recent weeks. Representing the teams working on two of the relevant themes in CREDS (Decarbonisation of the Steel Industry and Materials & Products), we have composed our thoughts on the matter here.
Proponents of the mine claim that it will lower greenhouse gas emissions by reducing imports of coking coal from the USA, Russia, and AustraliaOpens in a new tab to blast furnaces in the UK and EU. We estimate that transport emissions from the large coking coal mines in West Virginia, USA, to the large integrated steelworks at Port Talbot in South Wales are in the region of 62 kgCO2e per tonne, and that these would be reduced to around 9 kgCO2e per tonne for the proposed transport route from Cumbria. This reduction is only 1.8% of the emissions that arise from using that coal in steelmaking. The reduction increases to 5.4% if it avoids transport from Australia, however the share of coking coal imports to the UK has been moving from Australia to the USA in recent years, and this trend will only increase if the International Maritime Organization implements proposed carbon tax or “feebate”Opens in a new tab schemes to reduce shipping emissions.
It should be noted that this analysis does not include the emissions overhead associated with developing a new coal mine and its ultimate decommissioning, rather than continuing to use existing mines. Crucially, it also does not account for the longer-term implications of sending out the message that opening new coal mines is acceptable in the UK, particularly in the same year that the UK hosts the UN’s Climate Change Conference, COP26.
Blast furnaces run continuously for long (e.g., 25-year) “campaigns” between expensive overhauls. The government must be careful not to create the conditions for unabated blast furnace use to continue into new campaigns. The Climate Change Act in the UK does not only provide a net-zero emissions target by 2050, but importantly establishes five-yearly carbon budgets. It is vital to reduce cumulative emissions between now and 2050, but encouraging the continued operation of blast furnaces may jeopardise these targets. The Climate Change Committee has advised the government to target near-zero emissions from steelmakingOpens in a new tab in the UK by 2035.
Instead of transporting coal thousands of kilometres across the ocean or building new coal mines, the UK could take a more forward-thinking approach to steel production, by increasing reuse and recycling and investing in new low carbon steelmaking technologies.
Opportunities exist for reducing the UK’s demand for steel, whilst maintaining levels of service through material efficiency in both the production and consumption of steel. Strategies can involveOpens in a new tab optimising design of steel products, lightweighting, improving yields and recovering scrap for reuse on the production side, whilst steel consumption can be reduced by improving product longevity, and encouraging repair, remanufacture, and product sharing. In provisional analysis of material efficiency savings in the UK steel sector, our scenarios achieved reductions of between 16-20% in the cumulative greenhouse gas emissions of the sector from 2016-2050 (in addition to savings from technological interventions).
Early action on material efficiency is possible and could be disproportionately effective, given it would reduce the cumulative emissions from the sector at the early stages where emissions intensity is greatest. A scenario of earlier material efficiency further reduced the cumulative greenhouse gas emissions of the scenarios by an average 6%. Earlier material efficiency could also help bring the steel industry closer in line with the sectoral carbon budgets outlined by the CCC, reduce reliance on less proven technologies such as CCS and ease demands on hydrogen supply, particularly in light of the likely cross-sectoral competition for these vectors by 2050.
Steel is highly recyclable, and ferrous scrap can be melted down to make new steel in electric arc furnaces, which can be powered with zero-carbon electricity from renewables. In the UK we produce around 34% of new steel from scrapOpens in a new tab compared with 54% in the EU, and yet we are by far the largest scrap steel exporter in Europe, exporting millions of tonnes of ferrous scrap each year to countries such as Turkey, where industrial electricity prices are much lower. This could be avoided by introducing an export tariffOpens in a new tab on scrap steel, trialling and deploying measures to reduce contamination in steel recyclingOpens in a new tab, and ensuring that the cost of carbon applies across the entire economy, including cross-border flows of goods.
One promising zero-carbon steelmaking technology is hydrogen direct reduction of iron, which avoids all use of fossil fuels and instead produces only water as a by-product. Direct reduction of iron (DRI) using natural gas is a mature technology with over 100 DRI plants, pdfOpens in a new tab (15 pages, 4.3 MB) in operation around the world, and so using hydrogen is a case of fuel switching in proven technology. Hydrogen DRI is already being trialled by SSAB in Sweden, and the UK risks being left behind if it does not invest in similar development efforts. To create a market for hydrogen in the intervening period while existing blast furnaces complete their current campaigns, hydrogen injection could be used in blast furnaces to reduce the carbon intensity of steel production. This is already being trialled in GermanyOpens in a new tab by ThyssenKrupp.
Our research suggests that the marginal abatement cost of decarbonising UK steel production using hydrogen-based steelmaking will be less than the traded price of carbon by 2030 at the latest, and by the mid-2020s with central carbon price projections. This analysis uses the UK government’s recent projections of energy system technology costs and carbon prices, and accounts for the energy storage requirements of providing a firm supply of zero-carbon electricity and hydrogen.
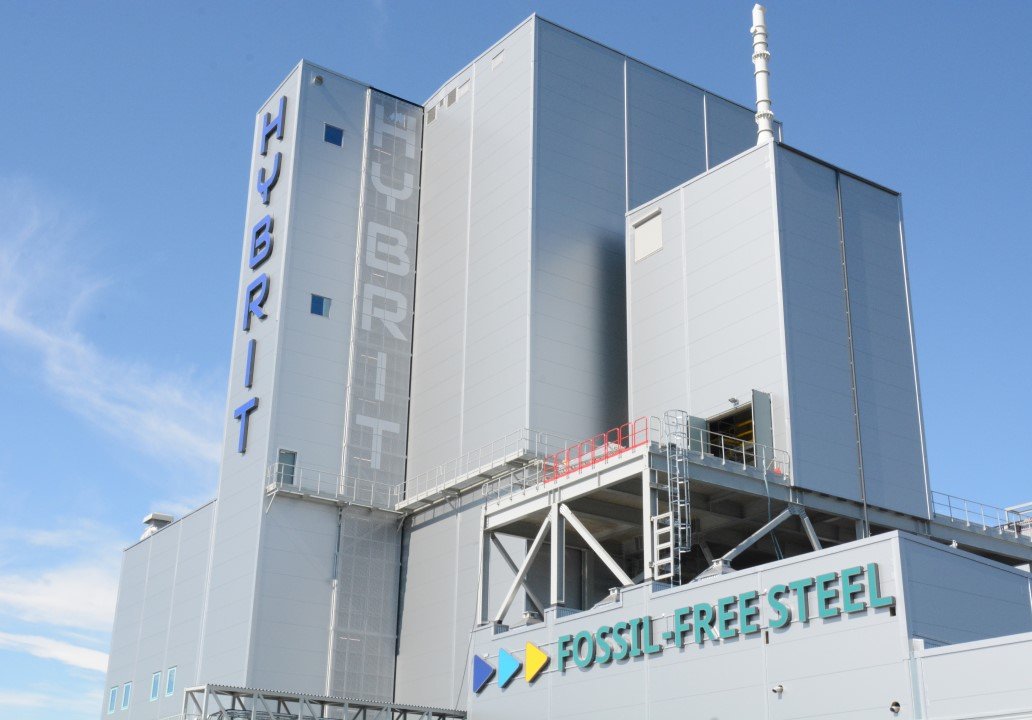
The firm behind the mine, West Cumbria Mining, has said that the mine will create 500 jobs, 400 of which would be filled by people from the local area. However, given that the UK has committed to ending unabated coal generationOpens in a new tab by 2024, and that the Climate Change Committee has advised the government to target near-zero emissions from steelmaking in the UK by 2035, these would be precarious jobs in an industry with no long-term future. Others have noted that the false dichotomy of “prosperity versus the environment”Opens in a new tab is conspicuously evident in Cumbria, which has suffered from devastating flooding in recent years.
Jobs are vital to a region’s economy, and Cumbria has been hit hard in recent years with the closure of a large chemical works and downsizing at the Sellafield nuclear facility (only 8 km from the proposed mine location). However, the area has a precious resource that will be vital to the entire economy as we move towards net-zero: the right conditions for offshore wind.
The latest offshore wind licensing round included a seabed bidding area just off the coast of West Cumbria. While no bids were awarded in that area this time, partnerships between offshore wind developers, the steel industry, and local landowners could make future bids more attractive and lead to jobs in both sectors.
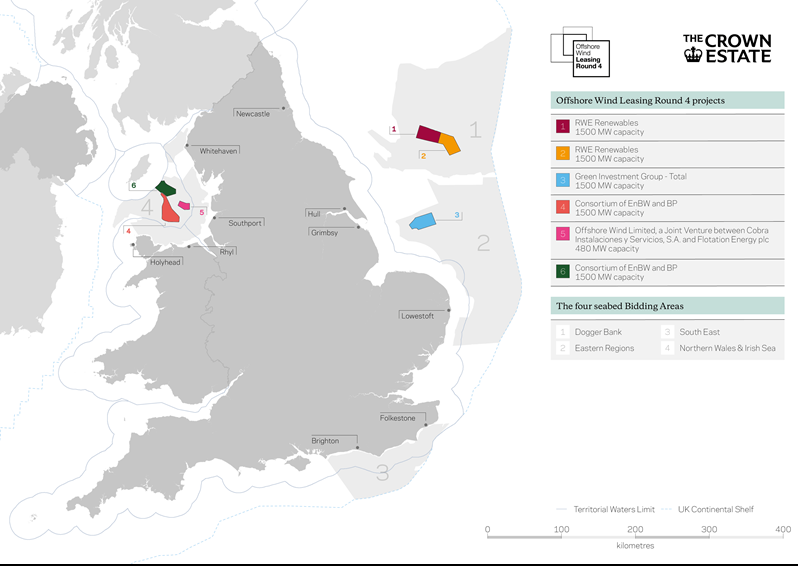
In the future steel industry, diversification of production facilities could be advantageous to reduce transmission requirements for electricity and hydrogen. Following this line of thought, the government could consider encouraging the deployment of fossil-free iron and steel production sites in areas such as West Cumbria which are fortunate to have the right conditions for offshore wind. Instead of exporting coal, perhaps Whitehaven could manufacture and export green steel, or zero carbon iron briquettes for use in steelmaking facilities elsewhere.
Prioritising material efficiency also provides employment benefits in supporting secondary materials markets. Analysis from Green Alliance has assessed the job creation potential of circular economy activities (not limited to the steel sector), estimating the creation of over 200,000 gross jobs by 2030 and reducing unemployment by 54,000Opens in a new tab in a ‘current development’ scenario. Furthermore, there is evidence to suggest that jobs in these secondary industries would be more regionally dispersedOpens in a new tab, therefore acting to create jobs in those regions where unemployment is greatest. By contrast, in 2019 there were only 1,000 employees in the coal production industryOpens in a new tab in the UK (across all mine types). Other estimates indicate that renewable and energy efficiency industries could yield a job-intensity of around 5-10 jobs per million invested, moreOpens in a new tab than in fossil power sectors.
Banner photo credit: Reading Tom on Flickr