Imogen Stevens, Alice Garvey, John Barrett and Jonathan Norman
Summary
A recent study by CREDS researchers at the University of Leeds (Garvey et al., 2022), investigating how to achieve net-zero greenhouse gas emissions in the steel sector, found that:
- Technological solutions alone will not be enough to reach net-zero; material efficiency will also be necessary. Our analysis suggests that radical retrofit combined with action on material efficiency could contribute to achieving the Climate Change Committee’s (CCC) further ambition steel sector carbon budget.
- Of the technological solutions, we found that retrofit could have the most potential in the short term, followed by new best practice efficiency technology, fuel shifts, and the implementation of novel technologies in the long term, depending on the availability of breakthrough technologies. Under some scenarios, carbon capture and storage (CCS) may be required, but material efficiency can offer the potential to reduce the need for reliance on such technology.
- Early action in the implementation of measures is required for more significant emissions reductions. To achieve this, a clear vision in the form of sectoral budgets and government leadership is necessary.
Technology alone is not enough; material efficiency will also be required
The most effective scenario to reach net-zero includes a combination of technological and material efficiency solutions.
Material efficiency, making use of less inputs to produce the same or greater output, can be implemented in the production of steel through:
- the optimisation of design
- material substitution
- increased use of scrap steel
- reductions in weight
- an improvement in fabrication yields.
It can also be applied to the consumption of steel by extending the lifetime of steel products, ensuring products can be repaired more easily and encouraging shared ownership and use of products by consumers.
Our analysis suggested that a high ambition retrofit scenario carried out alongside material efficiency gains could help reach the CCC further ambition target.
Proposals for a new Cumbrian coalmine are being justified by the perceived need for future coking coal as feedstock to the blast furnace steel production route. However, the technical need for the mine has been extensively refuted, with estimates suggesting the domestic supply of coking coal would only reduce emissions associated with transport by 1.8% (Pimm et al., 2021). Similarly, the implementation of material efficiency options would reduce the future demand for the feedstock.
The figure below indicates that at a central level of ambition in the technology scenarios and assuming the Energy Transitions Commission (ETC) (2018) material efficiency estimate, most scenarios are in line with the core CCC budget, but further mitigation would be required to reach levels aligned with the ‘further ambition’ budget.
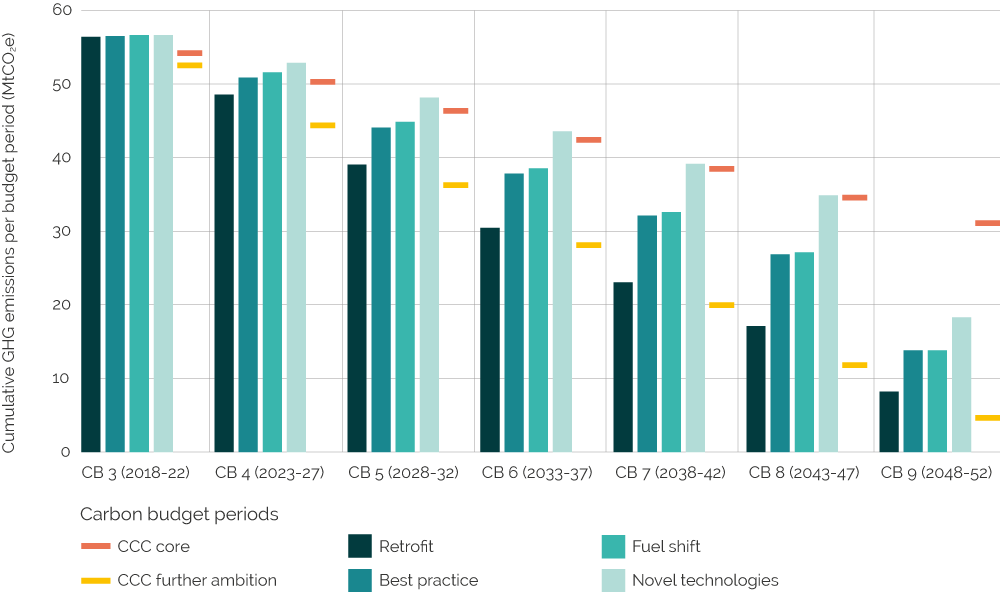
Image description
Bar chart shows the potential reduction in cumulative GHG emissions (MtCO2e) for each carbon budget (CB) period.
- From around 56 MtCO2e in CB 3 (2018–2022), emissions could reduce to less than 20 MtCO2e by CB 9 (2048–2052).
- The greatest reductions are likely to be through retrofit, which reduce to 8 MtCO2e during CB 9.
- Best practice and fuel shift could reduce to 14 MtCO2e for the CB 9 period.
- The core CCC ambition is to lower emissions to just above 30 MtCO2e by CB 9, with a further ambition to reduce to 5 MtCO2e.
Although hydrogen steelmaking has been proposed as a promising mitigation technology in the sector, it was not included in the ‘novel technologies’ scenario. This was due to: the complexity of representing this production route and its uncertainties, the variable estimates of the commercialisation lead times in the literature and the dependence on future availability of clean hydrogen in the UK.
There are some Hydrogen-Direct Reduction (H-DR) plants in operation, as highlighted in the Green Steel Tracker (Vogl et al., 2021) and ThyssenKrupp are trialling the use of green hydrogen in blast furnaces (Winter, 2020; Pimm et al., 2021). However, it has been suggested that production via H-DR could take 20 years for commercialisation (Åhman et al., 2019), or have most benefit after 2050 (Fischedick et al., 2014). Whilst there are 23 hydrogen steelmaking projects being demonstrated in Europe, there are no clear proposals for the same in the UK (ECIU, 2021). For a comprehensive assessment of the potential application of hydrogen to steelmaking, see Pimm et al. (2021a). To drive material efficiency, working with the steel sector alone is insufficient. Policy must also account for corresponding sectors such as construction.
Policy options include:
- Creating business opportunities for deconstruction and reuse of steel. This can be done through the creation of standards for the reuse of steel within the construction sector, where there is currently large untapped potential (Peake et al., 2018). Information on suppliers and detailed guidance on designing and building with reused steel is needed alongside this (Densley Tingley et al., 2017). Government leadership is important in making this transition, therefore the government should take the lead to create business opportunities and demonstrate the benefits of material efficiency through making the use of recycled and reused steel a requirement in public infrastructure (Densley Tingley et al., 2017; Peake et al., 2018).
- Increasing processing and domestic use of scrap steel. Currently large amounts of scrap steel are exported. Incorporating this into domestic production instead will improve material efficiency (Peake et al., 2018). This could be through methods such as a scrap stabilisation fund which companies can add to during times of high prices and remove from when prices are low in order to keep prices stable and ensure the use of scrap steel is profitable (Yellishetty et al., 2011). With the creation of more substantial secondary material markets both in the steel industry and other sectors, the UK could provide 54,000 net jobs (Peake et al., 2018).
- Extending product lifetimes and encouraging shared ownership. Extended lifetimes of products can be achieved through methods such as extended producer responsibility including longer warranties and repair services, e.g. via product standards or regulation such as the EU Right to Repair legislation. Product sharing aims to make more efficient use of products over their lifetime through strategies such as encouraging shared ownership and libraries of things (Cherry et al., 2018). In the steel sector this could be particularly applicable to vehicles and home appliances. Overall public opinion on this has been shown to be positive (Cherry et al., 2018).
Current technologies, especially retrofit, could have high potential to reduce emissions
Four technologies that are currently able to reduce emissions within the steel sector were analysed in the paper:
- Retrofitting existing systems with best available efficiency technologies.
- Replacing existing equipment with new, best practice technology.
- A fuel shift, moving to a larger share of electric arc furnace (EAF) production and away from blast furnace and blast oxygen furnace (BF-BOF) production.
- Novel technologies are those that have the potential to offer substantial emissions reductions but are not currently commercially viable or operational at larger scales in the UK.
Each of these scenarios were conducted at three levels of ambition – high, central and low depending on the speed of the changes taking place.
The results were compared to the CCC core and further ambition targets. The core measures would allow the UK to reduce emissions by 80% by 2050 compared to 1990 levels, while the further ambition scenarios have the potential to reach a 96% reduction by 2050 (CCC, 2019).
Retrofit was found to have the most potential to lower greenhouse gas emissions in the steel sector up until 2050, demonstrating between a 54 and 64% reduction in absolute emissions. The best practice technology scenario could deliver between 31 and 39% reductions, whereas fuel shift could account for 11–55% reductions, and novel technology 16–41% reductions. These findings are constrained by the top-down nature of the modelling, and limited awareness in the literature of the types of technologies already implemented by industry.
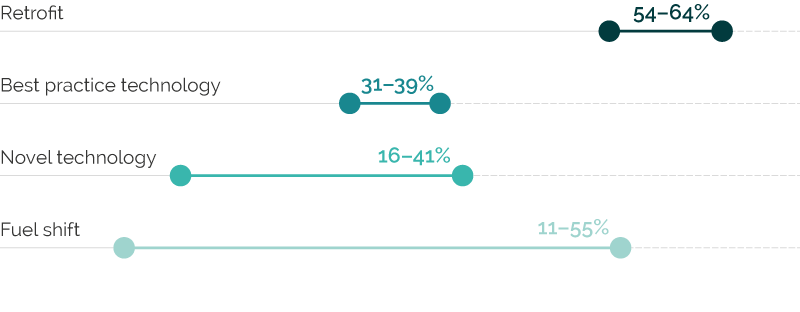
Image description
Relative emissions reduction potential: retrofit 54–64% reduction; best practice technology 31–39% reduction; novel technology 16–41% reduction; fuel shift 11–55% reduction.
Additionally, there is the potential that CCS will be required, especially if there is continuing use of Blast Furnace-Basic Oxygen Furnace (BF-BOF) production. However, material efficiency can offer the potential to reduce the need for reliance on such technology and should be a key component of policy decisions.
Large-scale adoption of technology should consist of instruments to provide incentives for uptake and to compensate for the higher costs. This will also be important to ensure firms remain competitive and to prevent carbon leakage.
Policy options include:
- Tax schemes. Incentives can be offered to companies through tax schemes to reduce the costs associated with new technology. This could operate in a similar way to the current Climate Change Agreements, but conditional on the uptake of technology to reduce emissions.
- Subsidies. Subsidising low-carbon technology to encourage uptake can reduce risks associated with costs and investment (CCC, 2019). These subsidies can be reduced over time as technology becomes widespread and more affordable.
- Investments. As investment in technology grows, the costs associated with it decrease, allowing for more widespread adoption (Mathews and Baroni, 2013). Encouraging investment is therefore important in encouraging the uptake of retrofit technology. There are only one or two investment cycles remaining in the steel sector before 2050, and therefore change needs to be made as soon as possible (DECC and BEIS, 2015).
- Research, development and demonstration of new technology. Significant investment in new technology will still be required for the long term (IEA, 2020). In the case that CCS becomes necessary, further action on development and deployment is needed to ensure it is viable (CCC, 2019). The existence of HYBRIT, a Swedish public-private partnership between steel companies and a state energy company to demonstrate the feasibility of hydrogen in steelmaking, provides an example of how technology can be demonstrated with government support (Pei et al., 2020).
Overall, stronger government intervention is recommended in order to encourage decarbonisation and help provide long-term financial stability for the steel sector by reducing costs incurred in the process (Webb, 2021).
Early action is necessary
Stronger support shown through the above recommendations would help reduce emissions from the production of steel itself rather than after they occur such as through emissions trading schemes. Taking action early to implement technological and material efficiency solutions will allow the steel sector to reach CCC core emissions budgets.
The UK steel industry is also of regional importance, with one third of jobs in the sector found in Northern England (Webb, 2021); policy to decarbonise could therefore have vital importance in supporting the so-called ‘levelling up’ agenda and economic recovery post-pandemic.
Policy options include:
- Sectoral budgets. More formalised sectoral carbon budgets could provide a useful framework within which policy can be set and progress assessed (Bataille et al., 2016). This could be achieved, for example, through expanding the role of the Climate Change Agreements, aligning targets with decarbonisation to meet 1.5°C.
- Government leadership. Leadership in the context of the energy transition is important. Coherent vision and ambition are necessary to mobilise others to change by providing direction and legitimacy (Grin et al., 2018). By implementing the above-mentioned policies in a timely manner, government can incentivise earlier action to decarbonise the steel sector.
References
Show all references
- Åhman, M., Olsson, O., Vogl, V., Nyqvist, B., Maltais, A., Nilsson, L.J., Hallding, K., Skånberg, K., Nilsson, M., 2019. Hydrogen steelmaking for a low-carbon economy: A joint LU-SEI working paper for the HYBRIT project. EESS report no 109 and SEI working paper WP 2018-07. Stockholm Environment Institute, Stockholm, and Lund University, Lund.
- Bataille, C., Waisman, H., Colombier, M., Segafredo, L., Williams, J. and Jotzo, F. 2016. The need for national deep decarbonization pathways for effective climate policy. Climate Policy, 16: S7–S26. doi: 10.1080/14693062.2016.1173005
- Cherry, C., Scott, K., Barrett, J. and Pidgeon, N. 2018. Public acceptance of resource- efficiency strategies to mitigate climate change. Nature Climate Change, 8(11): 1007–1012. doi: 10.1038/s41558-018-0298-3
- CCC, 2019. Net Zero: The UK’s contribution to stopping global warming. London: Climate Change Committee.
- Densley Tingley, D., Cooper, S. and Cullen, J. 2017. Understanding and overcoming the barriers to structural steel reuse, a UK perspective. Journal of Cleaner Production, 148: 642–652. doi: 10.1016/j.jclepro.2017.02.006
- DECC and BEIS (Department of Energy and Climate Change and Department for Business Innovation and Skills), 2015. Industrial decarbonisation and energy efficiency roadmaps to 2050: Iron and Steel. London: Crown Copyright.
- ECIU (Energy and Climate Intelligence Unit), 2021. Stuck on the starting line: How the UK is falling behind Europe in the race to clean steel. London: ECIU
- Fischedick, M., Marzinkowski, J., Winzer, P., Weigel, M. 2014. Techno-economic evaluation of innovative steel production technologies. Journal of Cleaner Production, 84: 563–80. doi: 10.1016/j.jclepro.2014.05.063
- Garvey, A., Norman, J. and Barrett, J. 2022. Technology and material efficiency scenarios for a net zero UK steel sector. Journal of Cleaner Production, 333: 130216. doi: 10.1016/j. jclepro.2021.130216
- Grin, J., Hassink, J., Karadzic, V. and Moors, E.H.M. 2018. Transformative leadership and contextual change. Sustainability (Switzerland), 10(7): 1–14. doi: 10.3390/SU10072159
- IEA, 2020. Iron and steel technology roadmap. Paris: International Energy Agency.
- Mathews, J.A. and Baroni, P. 2013. The industrial logistic surface: Displaying the impact of energy policy on uptake of new technologies. Energy, 57: 733–740. doi: 10.1016/j. energy.2013.05.048
- Peake, L., Brandmayr, C. and Klein, B. 2018. Completing the circle: Creating effective UK markets for recovered resources. London: Green Alliance.
- Pei, M., Petäjäniemi, M., Regnell, A. and Wijk, O. 2020. Toward a fossil free future with HYBRIT: Development of iron and steelmaking technology in Sweden and Finland. Metals, 10(7): 1–11. doi: 10.3390/met10070972
- Pimm, A., Garvey, A., Norman, J., Gale, W., Richardson-Barlow, C. 2021. Cumbria mine: Is there a technical need for new coal mines in the UK? Oxford: Centre for Research into Energy Demand Solutions.
- Pimm, A.J., Cockerill, T.T., and Gale, W.F. 2021a. Energy system requirements of fossil-free steelmaking using hydrogen direct reduction. Journal of Cleaner Production, 312: 127665. doi: 10.1016/j.jclepro.2021.127665
- Vogl, V, Sanchez, F, Gerres, T, Lettow, F, Bhaskar, A, Swalec, C, Mete, G, Åhman, M, Lehne, J, Schenk, S, Witecka, W, Olsson, O, Rootzén, J., 2021. Green steel tracker, Version 04/2021. Stockholm Environment Institute (SEI) and the LeadIT Secretariat.
- Webb, J. 2021. Forging the Future: A vision for northern steel’s net zero transformation. Institute for Public Policy Research (IPPR) North.
- Winter, O. 2020. Green hydrogen for steel production: RWE and thyssenkrupp plan partnership. Essen: RWE.
- Yellishetty, M., Mudd, G.M., Ranjith, P.G. and Tharumarajah, A. 2011. Environmental life- cycle comparisons of steel production and recycling: Sustainability issues, problems and prospects. Environmental Science and Policy, 14(6): 650–663. doi: 10.1016/j. envsci.2011.04.008
Publication details
Stevens, I., Garvey, A., Barrett, J. and Norman, J. 2021. Policy options for a net-zero emissions UK steel sector. CREDS Policy brief 018. Oxford, UK: Centre for Research into Energy Demand Solutions.
Banner photo credit: Alireza Attari on Unsplash